Responsible Care
Product Safety Mechanism (chemical substance management from design development)
At each stage of product development, from research and exploration to prototyping and mass production, DKS conducts surveys of laws and regulations as well as evaluations of environmental impact, and carries out design and development with the utmost consideration for product safety. In addition, by introducing a chemical substance management system, we conduct GHS1 classification, check laws and regulations, create multilingual SDS2 and labels, investigate substances contained in items such as our products, and are promoting the appropriate communication of information about our products.
- Globally Harmonized System (GHS) of Classification and Labeling of Chemicals
- Safety Data Sheet (SDS): A sheet containing information on the properties and handling of chemicals when transferring or providing them to other business operators
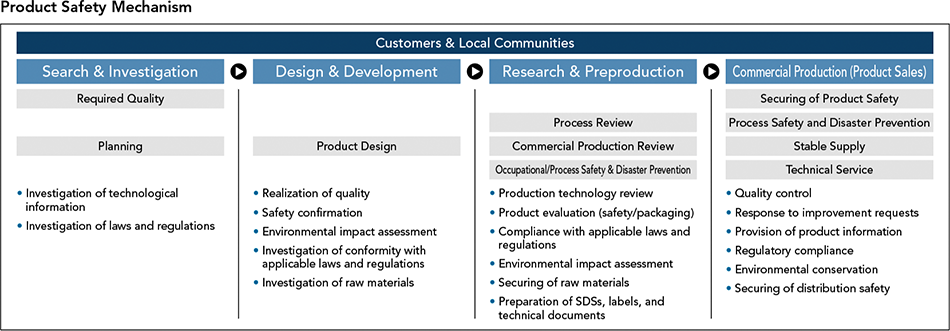
Occupational Safety Initiatives
Continuous improvement through occupational safety and a health management system
DKS recognizes that ensuring the safety and health of our workers is the foundation of our business activities, and we have established policies in the “Environmental Conservation, Health and Safety Management Regulations.” Since August 2018, we have been working to acquire Occupational Safety and Health Management System (OSHMS) certification, and following the Yokkaichi Branch and the Ohgata Branch, the Shiga Branch acquired JIS Q 45100 certification in December 2021. In order to further improve the level of occupational safety and health, we will continue to revise the OSHMS manual and related regulations, as well as create and revise manuals on health management.
Implement hands-on safety education
A hands-on training device was installed at the safety training center opened in February 2017 at the Yokkaichi Branch Kasumi Plant to increase sensitivity to abnormalities and dangers. In addition, we have introduced a simulated mini-plant, which can actually be operated, so that employees can understand the basic principles of equipment and processes. Using these facilities, 54 employees got hands-on safety training in fiscal 2021.
In the future, we will continue to conduct training to convey the importance of safety knowledge and stable operations, and to raise individual safety awareness.
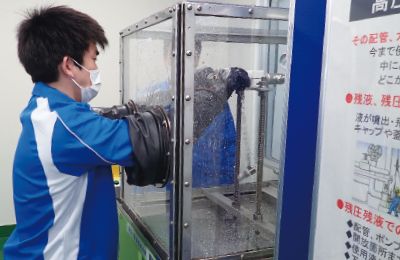
Initiatives for Logistics Safety
DKS entrusts external vendors with its logistics operations that involve product storage and transport. However, in adherence to the spirit of Responsible Care, our activities are guided by our stance that we will secure logistics safety and preserve the environment, as well as offer to customers guarantees of logistics quality and service delivery, among other principles. We work in close collaboration with our vendors to promote initiatives for logistics safety to realize these goals.
One particular aim we have is to eliminate accidents in logistics. To achieve this, we hold regular committee meetings to share information, consult, and educate on maintaining safe transport and traffic order, understanding amendments to laws, following delivery operations’ safety and environmental standards, understanding shipping specifications, and other topics.
In addition, in the event that an accident occurs during the transport of chemicals, so that drivers can take proper measures, we provide Yellow Cards* that indicate the Emergency Response Guidebook (ERG) number and the UN number as well as Container Yellow Cards indicating the same on the product labels.
- * An emergency contact card used when products are being delivered. In preparation for the event that an accident occurs during the delivery of chemical substances, this emergency contact card indicates the measures that should be taken by the relevant people.
Initiatives for Disaster Prevention
Response in Emergency Situations (Conducting Disaster Prevention Drills)
As preparation in case an emergency situation arises due to fire or explosion, earthquake, leakage, power outage or other events, we have constructed a framework for disaster prevention at every branch and carry out repeated disaster prevention drills in accordance with fiscal year plans. We have also taken measures to prepare in the event of such accidents and have developed a disaster prevention manual for emergencies based upon the incidents of large-scale fires and explosions that have occurred at domestic chemical factories in recent years. Disaster prevention drills are also performed with the cooperation, and in unison, with local fire departments and/ or public fire brigades. We continue to work on disaster prevention activities that will prevent accidents and disasters specific to a chemical manufacturer so as to ensure that they do not occur in the first place.
Disaster Prevention Measure Investment
Fiscal 2021 investment into disaster prevention measures amounted to ¥1,152.7 million. Investments mainly went to measures to respond to explosions, fires and leakages, as well as measures to deal with aging equipment, and measures to improve occupational safety and working environments.
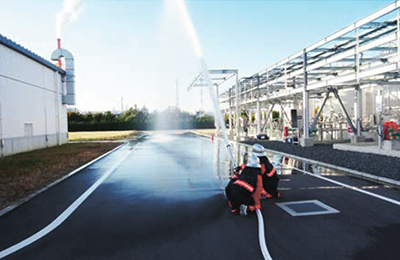
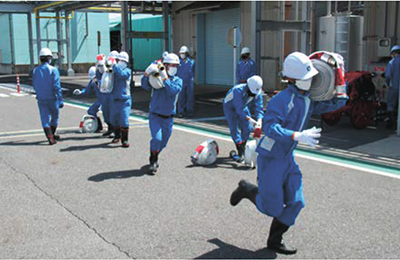
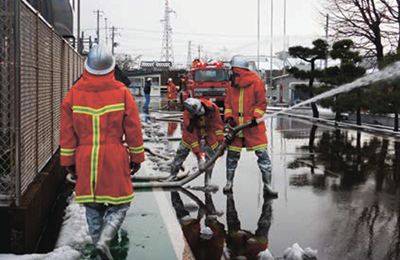