Quality Management
In order to meet the needs of customers and society and earn their trust, it is essential to improve the quality of the products and services we provide. At DKS, we consider quality from the four perspectives of “design and development,” “production,” “sales,” and “customer service,” and we are working to improve quality in cooperation with our customers and suppliers.
For details on quality and safety management, please visit our website (in Japanese only)
Quality Assurance/Quality Policy
As a chemical partner conveying the essence of high functionality for the future, we will provide customers with safer, higher-quality products that maximally contribute to the development of their business. To realize this, we engage in quality control using the PDCA cycle based on our fundamental quality assurance and quality policy in an effort to improve quality and customer satisfaction.
Fundamental Quality Assurance
- We establish quality-related management standards for each department that cover the entire process, from product planning to customer service through design and development, manufacturing and sales. Through the appropriate operation of such standards, we strive to provide high-quality products that are safe and reliable, maintain and improve product quality, and provide quality assurance for our customers.
- To effectively bring about quality assurance functions throughout the entire Company, we establish, operate, and maintain a quality management system and promote initiatives for on-going improvements.
- All our employees must observe this basic concept of quality assurance and carry out tasks in accordance with the Quality Assurance Management Regulations.
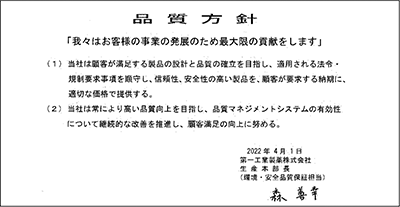
DKS Quality Assurance System
DKS promotes quality assurance activities by each department in charge of the process of product desig n and development, manufacturing, sales, and service. With the president as the highest quality assurance officer, the environment, safety, and quality assurance staff are responsible for raising quality assurance issues, formulating and recommending solutions, and overseeing the quality management system in order to ensure quality assurance. The QA Department General Manager oversees quality assurance in general and establishes and strengthens a quality assurance system through comprehensive coordination between other departments, and the Quality Assurance (PL) Meetings set the direction of quality assurance and quality control activities.
In line with diversifying customer demands and heightened requirements for product quality from a social perspective, we remain committed to working to ensure product safety and quality, as well as trying to prevent quality-related issues before they arise.
Quality Control System
DKS uses ISO 9001 as the basic tool of our quality management system to maintain and improve quality, and provide products and services that comply with customer requirements and laws and regulations by rotating the PDCA cycle. Furthermore, through careful daily activities (production management, corrective actions for nonconformities such as complaints and abnormalities, confirmation of effectiveness, change management, audits, education and training, etc.) and continuous review and improvement of the management system, we are working to improve customer satisfaction.
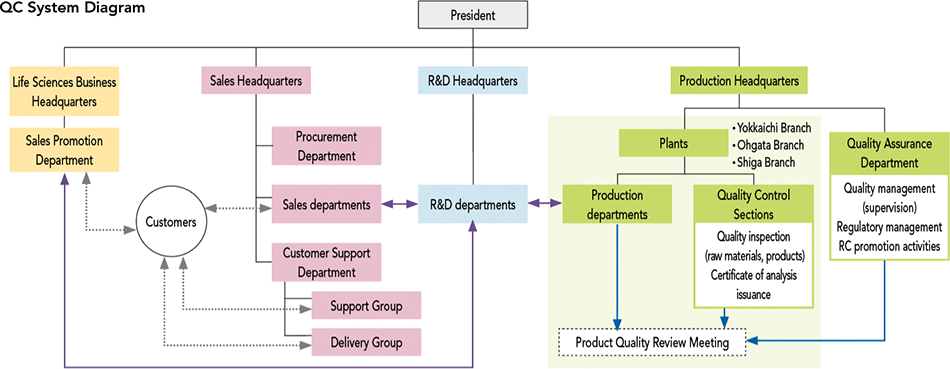